Precast in a new light
Thanks to the sustained efforts over the past few decades of everyone in the concrete industry from the architect to the specialist precaster, concrete is now very much the acceptable face of construction. Long gone are the ill-considered designs and details of the 1950s and 60s, which often led to unsightly weather staining, and in their place we are increasingly surrounded by the very best in facade shapes, colours and finishes. Certainly, not many construction materials can match its versatility and durability, with new techniques being constantly developed to increase the range of choices available to the client and architect. Facade surfaces can be retarded, polished, acid etched, or sand-blasted, with colour achieved by judicious use of white cement, pigments and coloured aggregates.
Though beauty can only be in the eyes of the beholder, there is little argument about the performance of these latest structures by members of the Architectural and Structural Precast Association, as a few examples clearly demonstrate.
Concrete education
When the Van der Meij College, Alkmaar, Netherlands, required an artistic facade for a new school building, Decomo took on the challenge. The snow-white colour was achieved by using white cement and a snow-white additive. The surface was polished and protected with a water-repellent coating after installation. From a distance, the facade looks like marble, but closer inspection reveals a tree-like relief structure with 3,046 leaves, 1,523 branches, 391 birds and 117 nests.
Back in the UK, and staying with education, the new storage facility for Oxford University’s ever-expanding Bodleian Library, which dates from 1602, involved stringent demands, starting with a minimum four-hour fire protection. Here, Decomo supplied architectural-grade precast sandwich panels with a grit-blasted finish to the external faces. Typical dimensions were 7.5 m long × 3 m high, each weighing 12.5 tonnes – some were larger, the biggest closer to 18.5 tonnes. From an aesthetic point of view, the panels to the front elevation – which houses the reception and offices – are the most interesting, with an attractive relief pattern simulating the appearance of books stored on shelves.
Commercial package
Occasionally, a project will call for both concrete and natural stone – perhaps the best of both worlds. At 40 Chancery Lane in London, for example, Sterling Services was able to demonstrate its expertise on a technically challenging £1.5m contract to provide a complete precast and natural stone facade package, with the primary facades consisting of precast columns clad in Oniciato Travertine quarried near Rome, Italy. Working closely with stone supplier Campolonghi, selected stone blocks from the quarry were cut, honed and dry-laid for viewing by the architect. They were then assessed for integrity, colour and range, with any changes being made immediately. Slabs were filled on the rear with colour-matched cement to close the surface. Each face was finished as honed and unfilled, and a display of the finished slabs inspected by the project team and the architect.
When the Wales-based insurer Admiral decided to build a new 245,000 ft 11-storey HQ building in Cardiff, Thorp Precast was selected to deliver the external envelope cladding package for the building on a full design, manufacture, supply and erect basis. The brief was to provide white Portland architectural precast concrete cladding with a high-quality surface finish featuring slightly exposed natural limestone aggregates. A series of pale reconstituted stone double-storey height vertical splayed mullions, with slender horizontal spandrel units, and large expanses of glass, allow maximum natural daylight infiltration to every floor. At lower level, a tall, colonnaded walkway running down the west side of the building is formed by a series of white architectural concrete columns and long-span spandrel units. All the precast cladding work was carried out without the need for external scaffolding and without the use of wet trades, providing significant construction time savings and major benefits in regards to health and safety.
Etched in memory
Somewhat unusually, a historical figure featured in Thorp’s involvement in the Pudding Mill Lane Pumping Station – an Olympic ‘Legacy’ project – the first operational building on the Olympic Park. The pigmented concrete walls of the building and perimeter were cast with a relief pattern based on the Victorian engineering drawings of Sir Joseph Bazalgette. They celebrate the engineering achievements of the sewer networks old and new, and contribute to a sense of civic pride engendered by this key infrastructure building. A detailed design brief was supported by a comprehensive set of implementation guidance documents for the Olympic Park that included requirements for sustainability, biodiversity, inclusive access, materials and security. Precast concrete cladding was chosen for its long-lasting robust finish and fast erection time, and Thorp’s ability to mould graphic representations into the concrete surface enabled the architect (John Lyall Architects) to make the building a subtle homage to Bazalgette.
Over the next three to five years, some one million square feet of new office, residential and retail space will be built at Cardiff’s Central Square scheme being developed by Rightacres Property and beginning with the distinctive One Capital Square. Early in the design process, Sterling Services introduced the idea of picture frame panels instead of columns and beams. This simplified and accelerated the design process. Furthermore, using a modular approach enabled any panel to go in any position in the building. This standardisation increased productivity and reduced installation time. In view of the large number of uses required from each mould, Sterling designed and tested resin-coated moulds that quadrupled their lifespan. In addition, insulation was pre-cut by the supplier and bespoke trailer frames were constructed to speed delivery. Before manufacture began, mock-up panels were produced for approval. Owing to the planned construction programme, a stockpile of aggregate was assembled at the quarry that would last six months, so ensuring consistency of product and colour. Sterling Services was awarded the contract by Wilmott Dixon to design, supply and install over 400 units in an acid etched white Portland finish. There are three sizes of window units used in varying combinations to achieve the striking appearance designed by Rio Architects.
Ship shape
As quality was the prime requirement on Torquay’s seafront, where the site of the burnt-down Palm Springs hotel was transformed into the Abbey Crescent mixed-use commercial and residential development, concrete was the natural choice. With a mix of commercial use and residential occupancy for the five storeys above, a transfer slab was needed over the retail development plus retaining walls to the rear of the building adjoining the cliff face. Cornish Concrete Products achieved these objectives with twin-wall construction to the rear to act as a retaining wall, and a mixture of beams, Demidec and hollow-core flooring acting as the transfer slab. The front elevation of the apartments features curved precast concrete cantilever balconies to the facade. The frame was crosswall construction, including the stair cores combined with the Deltabeams and hollow-core floor, punctuated with columns and Demidec lattice girder floors to the west end. However, viewed from the shore, it is not the hidden engineering but the sweeping lines of the precast facade panels that catch the eye, suggesting as they do the decks of a modern luxury cruise ship.
Currently, London’s Kings Cross – and particularly Pancras Square – is one of the busiest developments in Europe. Prompted by the start of work on the Channel Tunnel Rail Link in 2001 and the expansion and restoration of St Pancras Station, landowners, London & Continental Railways and DHL (formerly Excel), decided to develop the 67-acre site. Of the many projects that make up the development is Two Pancras Square, an impressive 11-storey 130,000 ft² building, the top three floors of which have been designed without a roof to facilitate a winter garden. The precast cladding units by Techrete have a high-quality ‘stone-like’ appearance, with sharp detailing.
What all these examples demonstrate is the increasing sophistication of architectural precast concrete and the growing confidence among clients and architects that if they can visualise something in the material then it is indeed possible.
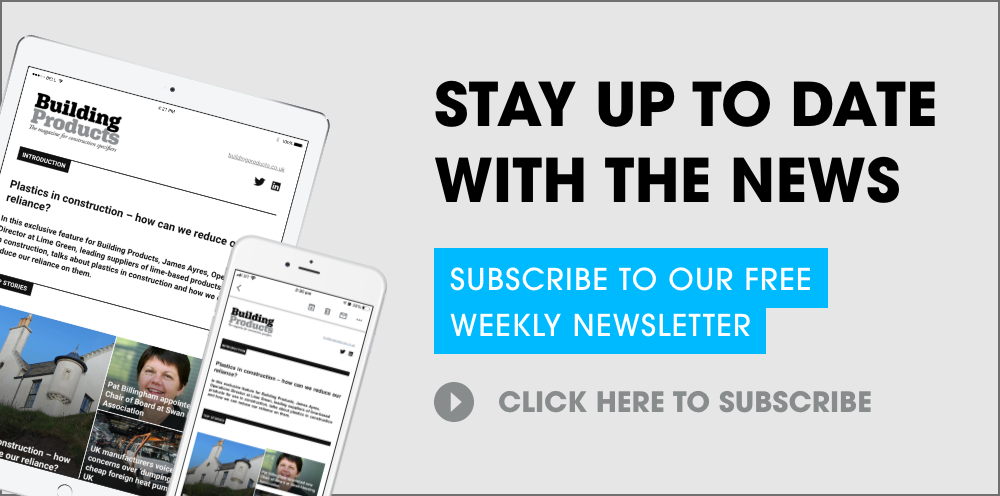