Plan to succeed
When everything’s going well, business is booming and the equipment that facilitates this is working properly, it can be easy to forget the importance of on-going maintenance. A well run building should do the opposite however, there is no room for complacency and leaving things to chance could back fire in a dramatic fashion. Wherever possible, we advocate planned maintenance – the reactive approach is a risky one, with high stakes should a serious issue occur.
Reactive maintenance is unavoidable – equipment can breakdown, even with the best laid plans. Ignoring maintenance and then reacting when something goes wrong, however, is a false economy. The price of extensive repair, replacement and higher running costs will, in almost every case, be more than preventing problems from occurring in the first instance. Money aside, breakdown or faulty operations could also pose health and safety risks.
Other factors that can increase the costs associated with reactive maintenance, include:
- Equipment downtime that could leave a business, or at least part of it, inoperable.
- Expensive part replacement, based on getting these parts as quickly as possible, rather than choosing the best supplier/price based on future need, not immediate requirements.
- Staff overtime/expensive call outs, where equipment has to be fixed immediately, whatever the time or day. Depending on the problem, the length of time required to resolve a problem may be indeterminate, meaning costs can escalate quickly.
- Shorter life expectancy of assets, with equipment deteriorating faster than necessary and small issues, turning into major problems.
All of this makes a reactive approach to maintenance a potential threat to budget control, which, for small businesses in particular, could be devastating if a particularly expensive breakdown occurred.
Plan ahead
Reactive maintenance’s downfall is Planned Preventative Maintenance’s (PPM) major plus point. One of the key benefits of PPM is that it can be budgeted for, with a monthly or quarterly costs attributed, to which a business can sensibly stick to. Apart from the physical price of this maintenance, in terms of labour and parts, workloads can be moved around/scheduled appropriately. This means that where equipment does have to come off-line it can be done so in such a way that minimises disruption, preventing losses due to reduced output and occupier discomfort. In public buildings, such as schools, leisure facilities, retail outlets and critical environments, preventing downtime is even more important.
In terms of cost savings, where HVAC equipment is concerned, often the easiest to quantify is improvements in energy efficiency. Specific savings vary depending on the equipment and the environment it operates in, but as a rough guide, a proper PPM schedule could see HVAC systems use 15-20% less energy than in a reactive maintenance culture.
PPM is also imperative in terms of keeping in-line with warranties especially in today’s market where some premium manufacturers are providing parts warranties in excess of three years. Manufacturer guidelines must at least be adhered to so that breakdowns that should not have occurred if equipment was looked after properly are covered. Ideally, PPM should go beyond this as individual environmental conditions have a bearing on equipment’s wear and tear. PPM reporting will also identify any operational bad practices which could damage the equipment or invalidate the warranty. Bad practices can then be simply addressed, usually with some onsite training.
Planned maintenance benefits include:
- Better, more efficient equipment performance
- Extended service life
- Minimised downtime and disruption
- Increased user/occupant satisfaction
- Ensures health and safety compliance
- Adds value by preserving and enhancing property assets
For HVAC systems in particular, which account for more than 40% of the energy usage in a commercial building, the considerable utility bill savings should more than covering the outlay of PPM. Add in the extended life of equipment, plus manageable maintenance costs and savings of as much as 50% could be achieved when comparing planned with reactive maintenance.
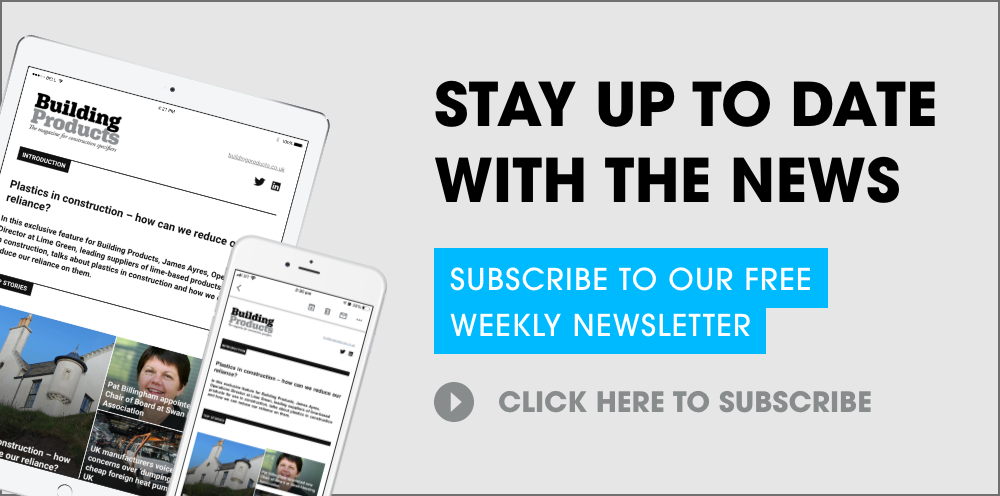