Victorian Sliders Invests Over Half a Million in a Glass Processing Line
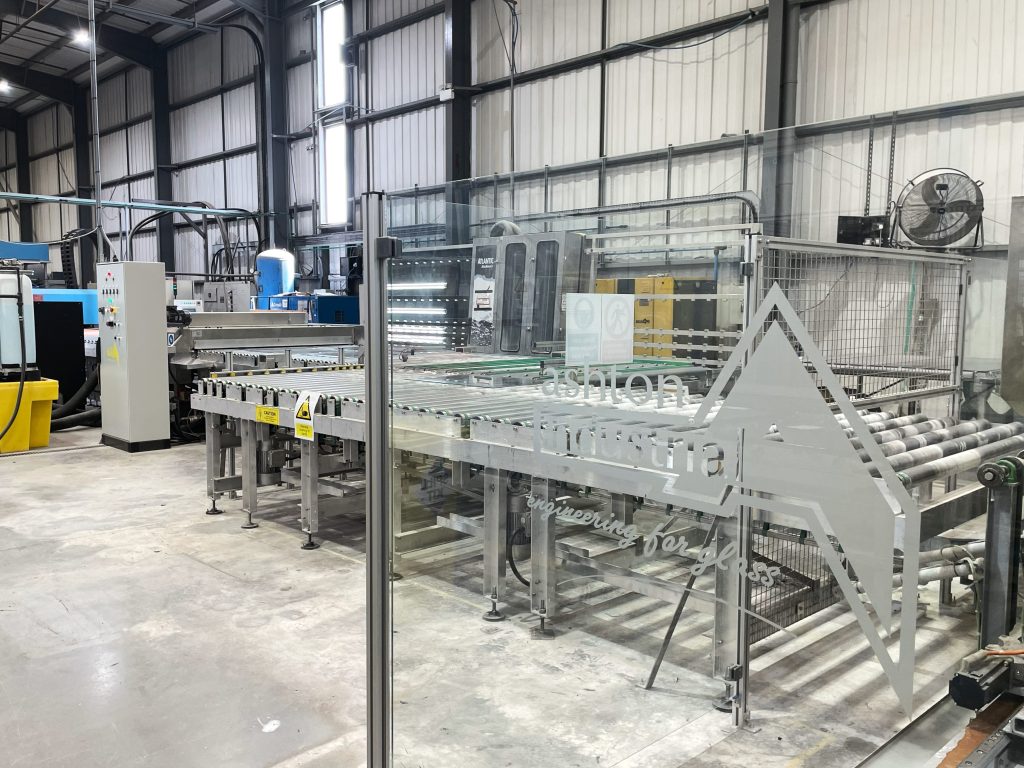
Victorian Sliders, Europe’s largest specialist PVCu sash window manufacturer, has significantly enhanced its glass processing capabilities with an investment exceeding half a million pounds in a fully automated seaming line from Ashton Industrial.
The investment in the Seamax seaming line marks a major step forward for Victorian Sliders, transforming the previously manual process of seaming, also known as arrissing, into a fully automated one. This technology ensures precise edge creation on glass, leading to superior quality double-glazed units.
An Ashton heavy duty UNIX cross belt arrisser with air floatation tables were also added to address the specials and shapes, and provides backup when the main line is being cleaned or serviced.
Victorian Sliders selected Ashton Industrial’s Seamax line after evaluating multiple providers. Key factors in their decision included strong industry recommendations, Ashton Industrial’s UK base, and the availability of ongoing engineering support. Processing glass horizontally reduces product handling and enhances safety, quality, and efficiency.
The new automated machinery significantly reduces production time and enhances accuracy and consistency. This advancement allows Victorian Sliders to meet growing demand while maintaining their industry-leading turnaround times.
Jason Powell, Operational Director, stated, “We chose the Seamax from Ashton Industrial for three main reasons: safety, quality, and efficiency. Our team values this investment and has taken additional pride in their workstations. We are confident this will enable us to meet market demands while maintaining our seven-day lead time.”
Steve Ashton, Managing Director of Ashton Industrial, added, “Working with Victorian Sliders has been great. Jason Powell and his team were decisive and clear about their needs, enabling a smooth collaboration.
Immediately convinced that this was the right direction for their tempering production at Victorian Sliders, there was no hesitation on their part. It’s always a pleasure to deal with people who are decisive and know what they want and things moved apace right from the start.
Jason and his team provided us with data on their glass sizes, required production volumes, and a layout of the available space in the facility, and between us we designed an ideal production flow incorporating direct infeed from their cutting and breaking line, through automatic arrissing and washing/drying, to automatic batch building and furnace feed.”
Nick Evans, CEO of Victorian Sliders, emphasised, “We’re committed to continuous innovation. This investment in our seaming line underscores our dedication to providing the highest quality products with exceptional efficiency.”
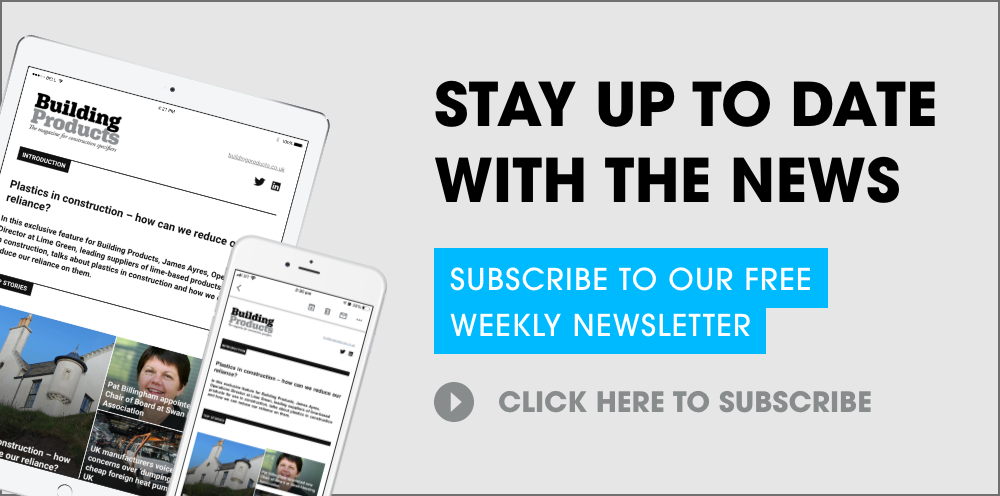