Alucast casts the dye with new £200,000 investment in testing capability

Delivering a single source manufacturing solution for aluminium castings is helping a Black Country foundry bounce back from the pandemic.
Alucast, which employs nearly 100 people at its factory in Wednesbury, has secured a number of new wins with major carmakers thanks to its ability to provide simulation, casting, machining and the latest testing facilities.
The latter has been strengthened even further, with the company investing more than £200,000 into creating a specialist Dye Penetrant offer, which is a form of non-destructive testing used to assess structural vehicle components and other parts for cracks.
This new line has been successfully operating for several months, with five members of staff fully trained on it.
“The automotive sector is always looking for faster production times and ‘right first time’ quality and this is what our latest investment is delivering,” explained Tony Sartorius, Chairman of Alucast.
“Cast and machined parts are cleaned and treated with a special, coloured penetrant liquid, which searches out minute cracks in the surface of the components. The parts are then left for a period of time, so that the penetrant can soak into any cracked areas, after which they are washed clean, which removes the liquid from the surface.
“A developer is then used on the part and essentially draws out the penetrant from the crack to reveal a coloured line if a fault exists. If cracks are evident, the part is scrapped.”
He added: “What this means to the customer is that they don’t lose time and experience additional costs that arise when a faulty part is sent out for secondary processes.”
Alucast offers sand, gravity and high and low pressure casting to a client base that spans automotive, construction products, electrification and hydraulics.
Part of the Manufacturing Assembly Network (MAN), the company had seen volumes dip during the pandemic, but, since lockdown was lifted, these have recovered through strong demand for its casting and machining capabilities.
The single source solution is proving extremely popular, with the Dye Penetrant testing joining additional complementary services, including casting simulation software, advanced laboratory facilities, X-ray, heat treatment and high-tech metrology.
This is helping the firm, which has recently been re-accredited to the TS16949 automotive quality standard, to create a strong reputation for supporting carmakers and tier 1s with structural lightweight parts for use in next generation vehicles and electric cars.
Tony went on to add: “We have to offer more than just casting if we are going to be successful in the modern auto industry and we started the move to a single source solution five years ago.
“Since that decision, we have invested nearly £3m into upgrading our core making facility and creating a new CNC machining shop with 5-axis capability, as well as the additional technology we have for testing and development.”
He concluded: “Servitization is a big area of potential for us, where customers can access individual services we offer, such as casting simulation and heat treatment, to solve specific production issues or to ensure quality compliance.
“The addition of a Dye Penetrant department is a perfect example of this and we are seeing a steady increase in companies using it to double-check their parts.”
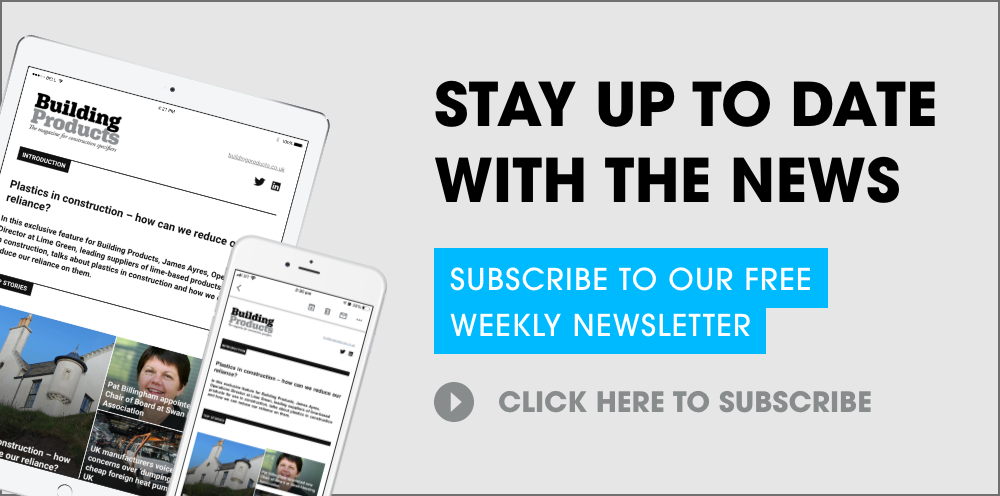