Britain’s manufacturers invest more than £500 million to end Britain’s housing crisis – targeting 75,000 sustainable modular homes by end of decade
Today Make UK launches a new trade body Make Modular, bringing together Britain’s leading modular housing manufacturers with a plan to solve the country’s housing crisis by delivering 75,000 affordable high-quality homes before the end of the decade.
The UK housing market is at a tipping point where it could transform into the most advanced housing manufacturing market in the world in under a decade delivering in excess of 75,000 new homes via modular housing. Make Modular members’ factories can produce a new home every 2 hours. These homes are near defect free with 97% less embodied carbon than traditional builds. Make Modular members have already invested more than £500 million in new factories, cutting edge processes, and state of the art technology.
The UK construction sector will have lost at least 25% of its workforce by between 2016-25. There is a major risk that by the next election construction has become the new haulage with economic competitiveness undermined by an ageing workforce leaving the industry. More than 2,000 new jobs have been created by Make Modular members in the last 3 years. By moving people off-site and into clean, safe, modern working conditions volumetric can rebuild the construction workforce bringing up to 50,000 new younger people into the workforce.
Uniquely in the construction sector, modular housing provides the opportunity to construct offsite and in regions where labour is available. Homes are then transported to the areas where demand for new homes is the highest. Current factories driving the start of the modular revolution are already located in the Midlands and the North of the country, providing highly skilled and sought after careers using the latest digital and automated technologies with innovative design bringing about the highest environmental credentials.
Stephen Phipson, CEO of Make UK said: “Imaginative and speedy solutions are required to tackle Britain’s housing crisis and modular housing could certainly play a significant part in helping local authorities deliver the challenging home building targets set for them by Government. But to make real significant progress, modular housing needs to have equal access to land for construction with many sites still favouring traditional modes of construction.
“Modular also needs to have the weight of Government procurement behind it using a joined-up approach including education, defence and housing to build much needed scale the UK’s modular industry.”
Modular housing manufacturers are also keen to accelerate the development of building regulations to match a new, more ambitious new normal when it comes to quality and energy across construction as a whole, driving forward the world’s biggest challenge of climate change.
Dave Sheridan, Chair of Make UK Modular said: ‘Modular housing has grown rapidly in the last few years. The establishment of our own trade body is the crucial next step in this process. As a natural partner to Government to solve the housing crisis, deliver the levelling up agenda, and combat climate change Make Modular will accelerate and advance the MMC agenda through one strong voice rather than a series of disparate ones.’
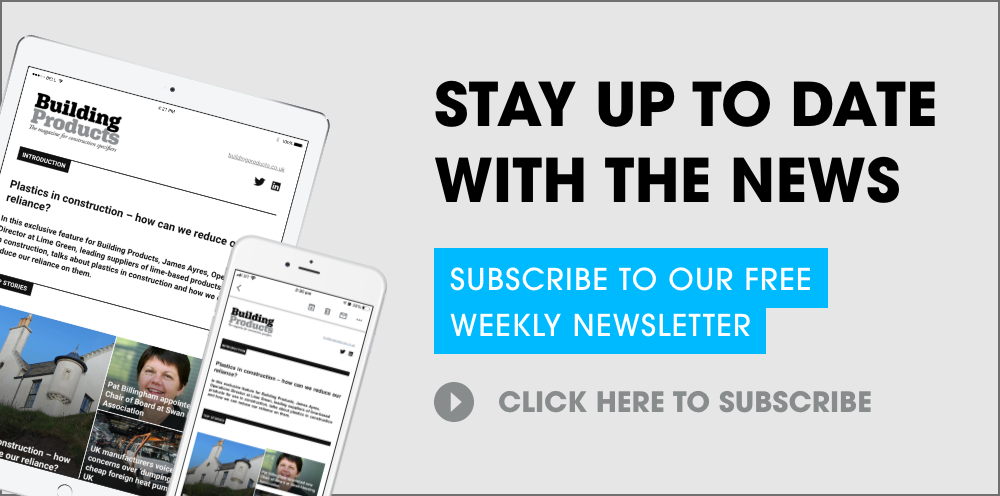