Forterra’s Challenges in the Face of the Housing Slump

In the wake of a persistent housing slump, brickmaker Forterra is grappling with declining demand and unexpected challenges. The third-quarter trading update from Forterra reveals that the company’s earlier optimism for an upturn in sales has faded, and it now anticipates a more subdued financial performance for the year. This article explores the key factors contributing to Forterra’s situation, including the decline in market demand and a reduction in brick despatches. We will also delve into Forterra’s strategic responses, such as mothballing factories and cutting production.
Declining Demand and Market Deterioration
A Disappointing Third Quarter
Forterra had initially anticipated a “modest” improvement in its second-half performance. However, the reality turned out to be quite different. The signs of market improvement witnessed in May and June did not persist into the second half of the year. Market demand significantly deteriorated in July and August, painting a challenging picture for the brickmaker.
A Look at the Numbers
Official figures illustrate the severity of the situation. Brick despatches in July and August were 16% lower than they were in June, and this figure plummeted even further compared to the same period the previous year, with a 28% decrease.
Future Expectations and Inventory Management
Caution for 2023
Forterra’s outlook for the future is marked by caution. The company foresees that demand in the coming year will be similar to the levels observed in 2023. This anticipation comes with a warning: they plan to restrict the production of bricks to align with sales, thereby preventing further inventory growth.
Mothballing Factories
As a response to the challenging market conditions, Forterra is taking decisive action. One such measure is the mothballing of its Claughton site in Lancashire. This is in addition to earlier announcements regarding the mothballing of the Howley Park site in West Yorkshire. These steps signify Forterra’s commitment to adapt to the ongoing challenges.
Cuts in Production
Apart from mothballing factories, Forterra is also trimming production at its aircrete business. These production cuts are part of a strategic move to streamline operations in the face of reduced demand and market uncertainties.
Financial Performance
Interim Results
In its interim results for this summer, Forterra reported a decline in revenue, which fell by 18% to £183 million for the six months leading to June. Pre-tax profit also took a significant hit, plummeting by 59% to £18 million.
Comparing with 2022
Contrasting the current scenario with 2022, there’s a substantial difference. In the previous year, Forterra reported revenue of £456 million, which marked a significant rise of 23% from the figures of 2021. The pre-tax profit also surged, growing by 28% from £57 million to £73 million.
Brickability’s Acquisition
While Forterra faces its share of challenges, another key player in the construction industry, Brickability, has made an interesting move. The construction materials distributor recently acquired cladding installation and remediation contractor Topek for £45 million. This acquisition might hold significant implications in the evolving construction landscape.
Brickability’s Own Challenges
In a trading update, Brickability indicated that its revenue for the six months leading to September would be 8% lower, amounting to £324 million. These results are also influenced by the housing slowdown, underscoring the broader impact on companies within the construction materials sector. Earnings for Brickability are expected to remain in line with the previous expectations at around £24 million.
The challenges faced by Forterra in the midst of the housing slump are indicative of the broader dynamics at play in the construction and building materials industry. The decline in demand, production adjustments, and a cautious outlook for the future present a complex landscape. Moreover, the acquisition by Brickability and its own challenges add another layer to the evolving narrative. As the industry navigates these complexities, Forterra’s strategic choices and adaptability will play a pivotal role in its future trajectory.
Frequently Asked Questions
What are the latest trends in cladding materials for construction projects?
As of 2024, some notable trends in cladding materials include the increased use of sustainable and recycled materials, the integration of smart technologies for energy efficiency, and a growing emphasis on modular and prefabricated cladding solutions.
How does the current regulatory environment impact the use of cladding in building construction?
The regulatory environment plays a crucial role in shaping the use of cladding in construction. Recent developments focus on enhanced fire safety standards, stricter compliance requirements, and increased scrutiny on the performance and composition of cladding materials, particularly in the wake of past incidents.
Are there any recent innovations in cladding technology that are gaining popularity in the construction industry?
Yes, innovations in cladding technology include advancements in self-cleaning surfaces, integration of photovoltaic elements for energy generation, and the use of high-performance materials with improved insulation properties. These innovations aim to enhance both functionality and sustainability in construction.
What are the key considerations when selecting cladding for energy-efficient building designs?
Key considerations for energy-efficient cladding selection include thermal performance, insulation properties, and the use of reflective or cool roof technologies. Additionally, choosing materials with a low environmental impact and a high degree of recyclability aligns with sustainable building practices.
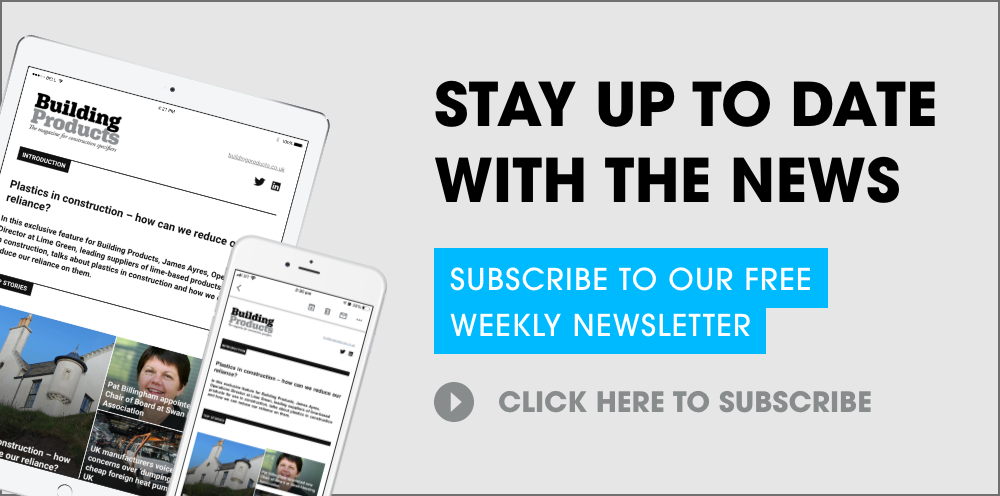