Inverted guidance
Over the past ten years, central Government has set numerous energy saving initiatives. Whilst some of these have been postponed – such as Zero Carbon Homes – sustainability is still at the forefront of modern construction in the UK.
Construction 2025 is one of many ambitious documents that aim to reduce CO₂ emissions. Along with lower construction costs, faster delivery and improvements in exports, Construction 2025’s main objectives is to place Britain at the forefront of modern construction whilst reducing its greenhouse gas emissions by 50%.
These energy saving objectives, and others like them, have emphasised the need for highly efficient insulation. To demonstrate its performance, an insulation U-value must be calculated to measure the heat loss in a building. Whilst a U-value can be easily created for traditional warm flat roof construction – where the insulation is placed below a water proofing membrane to shield against damp – there are numerous factors a contractor must consider when calculating the U-value for an inverted flat roof.
As inverted flat roof insulation is typically placed on top of the water proofing membrane to protect it from stresses such as freeze/thaw and condensation, rain water can flow around the insulation, subjecting it to moisture ingress. Commonly known as rainwater cooling, this additional moisture can result in substantial heat loss, causing the building to underperform, rendering initial calculations redundant. It can also alter the insulation’s lambda value, a calculation showing the rate at which heat transfers through one square meter of a building.
Since 1 July 2012, the British Board of Agrément (BBA) decided that all products that declare to have a thermal performance, such as insulation, must have a lambda 90/90 calculation. Also known as declared lambda, the 90/90 value refers to 90% of production achieved with a 90% confidence level.
Whilst declared lambda is an appropriate calculation for the insulation in warm flat roof construction, the system does not give an accurate U-value calculation when used in inverted flat roof projects as the additional moisture can seriously affect the insulation’s performance.
To mitigate this problem, the European Organisation for Technical Approvals (EOTA) agreed an industry standard to apply the requirements of the European Technical Approval Guideline (ETAG) 031-1 to inverted roof U-value calculations. This standard requires specifiers and manufacturers to quote lambda values whilst taking into account the effect the moisture ingress has on the insulation boards, through freeze/thaw and rainwater cooling of the deck. Only once this effect has been determined and calculated in accordance with British Standards EN ISO 10456, can a designed lambda value be created.
Although a designed lambda is needed to calculate how much insulation is required, we are seeing an increasing use by some specialists of declared lambda calculations only. This means the insulation thickness is minimised to meet the required U-value as environmental factors are not considered.
Using thinner insulation boards could result in the heat loss through the roof being greater than required by the design lambda, resulting in a performance gap between the expected efficiency of the insulation compared to its real world performance.
In order to avoid this, it is essential that the thermal performance of the insulation is calculated using design lambda, not declared lambda value. To remove any doubt, there are specialist energy efficiency advisors on hand to offer the technical advice required. By ensuring calculations are correct in the early stages of a project, it is possible to be much more certain a building meets its desired performance from the outset.
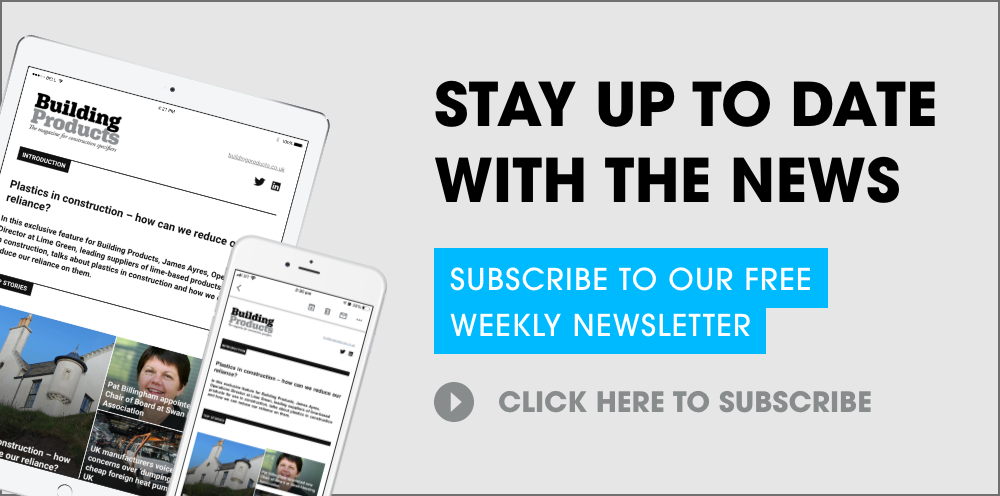