Maintaining integrity
Whatever the aspirations of the rooflight system – light transmission, thermal efficiency or sound insulation – the designer must take into account a whole host of elements including light, heat, ventilation, strength and maintenance. From infill types to glazing bar widths, it’s crucial to get each aspect of the specification right to deliver optimum performance throughout the system’s lifetime and prevent costly failures in the future.
Strong silent types
Specifying the glass type is one of the key stages of the process. With a huge range of infills available – including clear, translucent and opaque panels in glass, polycarbonate or GRP – the designer must consider the height of the building, the size of the rooflight and the use of the space below.
For domestic projects, price remains an important consideration and it’s important to choose the best performing glass to give excellent all year round comfort. Commercial projects have different considerations, but again emphasis should be placed on best value and availability to avoid long lead times and to keep costs down in the event of replacement.
When two sheets of glass are bonded together with an interlayer, this forms laminated glass. Although this glass is still breakable, it is actually a little stronger than in its original form, and simply cracks and remains in place due to the bonded interlayer. Commonly used in the motor industry for car windscreens, laminated glass is also used as single glazing for canopies, walkways, railway platform glazing and other unheated spaces.
Toughened glass is manufactured through a heating process that uses controlled thermal or chemical treatments to increase its strength compared with normal glass. When broken, the glass crumbles into small granular chunks of similar size and shape instead of splintering into random, jagged shards.
Wired safety glass enables classification to BS6206 Class C Safety Rating, while normal ‘wired glass’ is not suitable. Used since the end of the 19th century for overhead glazing, the wires hold together any broken pieces of glass providing a similar, but not as efficient function as the PVB interlayer on laminated glass. As a superior version of wired glass, the safety version provides fire resistance but care must be taken to ensure the system provides the required half hour or one hour protection.
A commanding performance
Historically, designers would resist the temptation to incorporate rooflights as they were put off by the misconception that rooflights would have negatively affected a building’s energy consumption. Today the opposite can be true with a high quality rooflight helping to cut energy costs and reduce the building’s use of electric lights.
With ever more stringent Building Regulations and end users demanding better performing buildings, the construction industry is switching on to the numerous benefits of roof glazing systems. On-going changes to Building Regulations Document L apply to domestic and commercial properties and refer to buildings as ‘dwellings’ and ‘non-dwellings’. In Part L 2013, the heat transfer through rooflights in domestic buildings must not exceed 2.0 W/m²K. For non-domestic buildings, the U-value limit for windows and rooflights is 2.2 W/m²K.
As there is no harmonised European standard or British standard for flat-roof glass rooflights or skylights, there isn’t any mandatory testing in the UK. As a result, the only way to prove suitability and compliance is through certification. Good advice would be to avoid companies who do not offer this level of technical back-up as Building Control Officers are increasingly vigilant regarding this issue.
Clean and clear
In addition to designing, specifying and installing rooflights properly, a periodical inspection of the roof will uncover any evidence of leaks into or around the glazing unit. As a result, rooflight designers should seriously consider cleaning and maintenance obligations before installation to ensure any glazing system can be safely cleaned throughout its life cycle.
It is important to clean both the glass and aluminium system to prevent the build-up of grime and debris in order to maintain good light transmission. In addition, any architectural finishes must be cleaned in accordance with the manufacturer’s instructions to ensure any warranty remains valid.
Whatever the project, it’s an age-old saying but with rooflights it is true – you get what you pay for. Avoid those dreary, cheap and cheerful plastic rooflight systems or you could be left facing years of rooflight trouble. High quality rooflight systems will combine a long design life with low maintenance to deliver exactly what the customer wants – a rooflight that is built to stand the test of time.
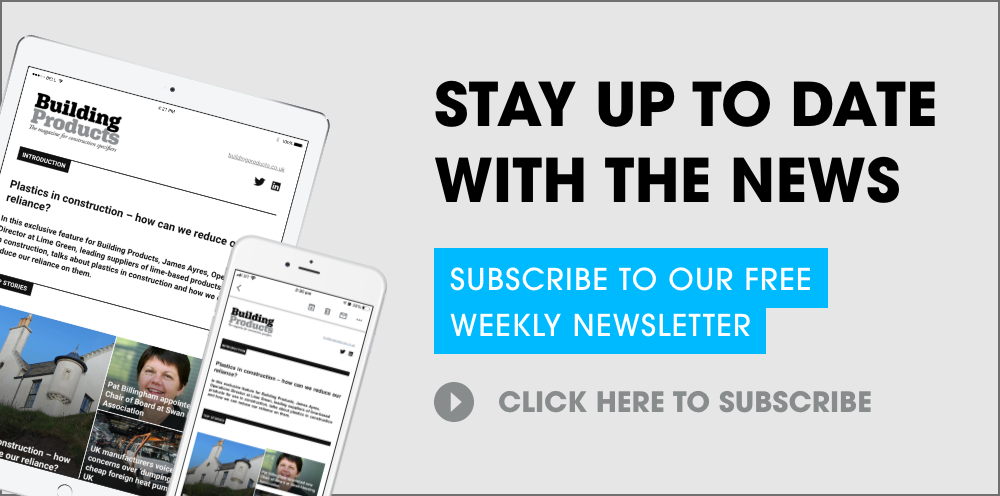