MD in Focus: Rob Glen from Access 360
Bilco UK, Profab Access and Howe Green together form Access 360, a division of Tyman UK & Ireland, which provides access solutions for roof, ceiling, wall and floor access products to the construction industry. Here, Building Products talks to the Managing Director of Access 360, Rob Glen.
Can you tell us about your working background?
I joined Access 360 as Interim Operations Director in June 2020. My main objective was to lead the operational and engineering responsibilities of the three contributory businesses to implement lean manufacturing, whilst simultaneously improving engineering design processes to achieve best working practice to ensure every customer receives the product and service they need.
Prior to this, I was the Managing Director of Don-Bur, designer and manufacturer of commercial vehicle trailers and rigid bodywork. My Engineering Degree and MSc in Manufacturing Business Management paved the way for my career in operations and engineering, with previous experience including roles within the Aerospace Division of Rolls Royce for a number of years and General Manager for one of the world’s largest suppliers of automotive parts.
What does your role as Managing Director entail?
As the recently appointed Managing Director of Access 360, my responsibilities include achieving a higher level of integration between the three businesses and their operating systems, ensuring we are not just supplying a product, but providing the complete solution each client requires.
This includes the successful implementation of a new ERP platform, which is driven by an agile configurator that can quickly and correctly define each unique specification, from sizing and formation, through to handle position and frame types.
What does your average day look like?
As you can imagine each day is extremely varied. My main responsibilities centre around identifying and executing the strategy of each business to support Tyman UK & Ireland’s dedicated growth objectives. Central to this are the Tyman core values that help guide us in our decision making and policy development.
This includes reviews of our quality and business systems to ensure they are fit for purpose, in addition to continuous innovation and product development to understand how we can continue to meet market needs to the best of our abilities.
Do you find it easy to attract the skills you need in your business?
COVID-19 has had a significant impact on the labour market across all levels, from manufacturing engineers on the shop floor, right through to senior level management.
It is extremely important that businesses have the capability and flexibility to meet the expectations and needs of today’s talent.
As part of Tyman UK & Ireland’s purpose and values, we are committed to understanding what matters to our current and future employees.
As part of this, we are dedicated to supporting the early stages of career development, which is why we are currently sponsoring an undergraduate through the final year of their Engineering Degree. This will place them in a strong position to accelerate their career with Access 360 when they graduate and support us in bolstering our new product development and engineering capabilities.
How are you positioning the business to do its bit to tackle climate change?
The Tyman 2030 Sustainability Excellence Roadmap details our action plan and outlines how Access 360 will achieve sustainable operations to deliver more environmentally friendly product and service solutions.
A key ambition of the Roadmap is accomplishing carbon neutral operational emissions (Scope 1 and 2) by the end of 2030. This will be accomplished by implementing a holistic approach to energy efficiency, including the deployment of renewable energy technologies, in addition to dedicated carbon removal projects.
The Sustainability Excellence Roadmap also outlines our aims to deliver 100% sustainable packaging by 2026, in addition to eliminating waste to landfill within the same year.
At brand level, we are proactively working to reduce the level of polystyrene within our product packaging, replacing it with starch-impregnated cardboard. This significantly improves the sustainability of our packaging, without compromising the quality of protection when the product is in transit.
We are also proactively investing in new procurement and engineering practices to achieve the highest content of recycled materials within our products, whilst simultaneously improving their recyclability.
As a result of this commitment, our Fire Rated and Non-Fire Rated riser doors are 98% recyclable, whilst the recycled content in our steel is currently between 20% and 25%, in line with the current European availability of scrap materials.
We are also identifying areas where we can further invest within each business to improve efficiencies as far as possible. This includes the procurement of new equipment, in addition to providing dedicated training to ensure our teams are operating in the most effective way.
What type of leader would you say you are?
Leadership is about getting the best out of your people. It’s essential to demonstrate humility and focus on the purpose of the business, whilst understanding what your employees need and how you can guide them.
In order to continuously progress and collectively develop, it is important for my team and I to inspire one another to do the best we can. As a result, we can achieve a culture that has values including to never be frightened of failure, but to learn from it and continuously strive to improve and succeed.
What do you do to switch off when you have spare time?
I previously restored a BMW M3, which I like to take on the road as much as I can. I’m also an avid sports fan and used to play frequently, although now I mostly watch it!
How is technology and innovation impacting your business and sector?
New technologies are completely transforming the design and specification stages for construction professionals. The adoption of our new interactive configurator will enable professionals to build and visualise products to bespoke specifications before converting them into a BIM model.
It is essential that we constantly innovate to meet market needs, and the introduction of these technologies will enable us to provide ultimate convenience by streamlining the specification stages for professionals.
We have also adopted the use of 3D printers to generate conceptual products, so that individuals can physically see how their bespoke specification will look, function and perform.
From an innovation perspective, we understand the importance of assisting the specification stages, but we also know the responsibility we have to support contractors in installing our products to the highest possible standard. This is particularly important for fire rated products where correct installation is paramount to achieving compliance and first-class performance.
This is why we have developed our new PRECISION Adjustable Frame, a revolutionary certified system that sets a new standard for innovation, fire performance and functionality, making installation on site safer, faster and simpler.
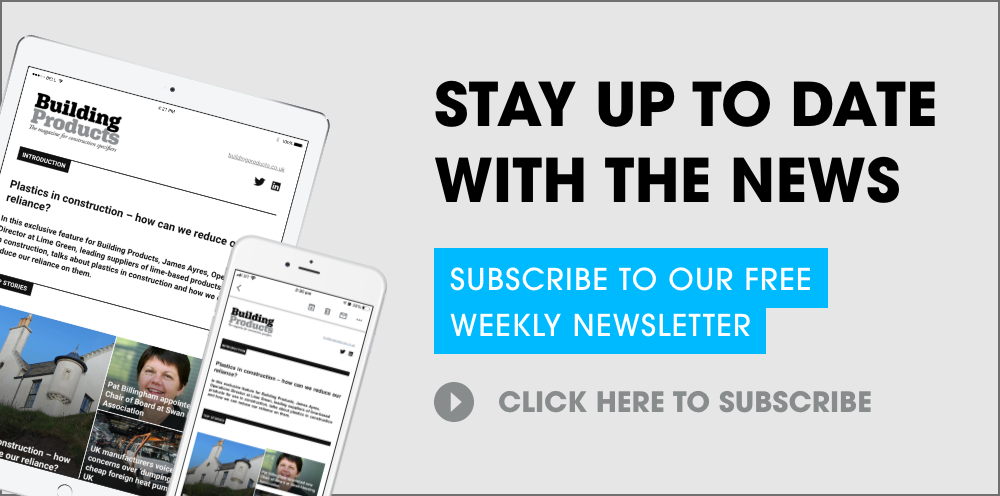