Sprayers answered
Conventional methods of plastering come with many drawbacks which the gypsum products industry has been striving to answer for some time. New developments in material technology and delivery now mean the solution is readily to hand – ready-mixed spray plasters (RMPs). These alternatives to traditional systems are more cost effective, faster, more consistent in quality, and cleaner, while ticking several boxes in terms of sustainability.
The benefits of RMPs are also scaleable – it doesn’t matter whether you’re a main contractor or small builder. Whether delivering extensions or tackling volume builds, using these products saves time and money, while delivering a premium finish that will pass the most stringent demands.
Fast application
The principal advantage of RMPs is speed. Application is up to three or four times faster than conventional methods, and drying times are fast enough to allow following trades to be at work within two days.
Up to 1,000 m² per week can be applied by a two or three man team. Thanks to the spray application, ceilings can be finished from floor level (up to a height of 3 m), obviating the need for scaffolding, steps or hop-ups and improving health and safety at no extra cost. Faster application also leads to better quality because it means the job requires fewer operatives on site, so it is far simpler to supervise the operation and achieve a consistent finish throughout the project.
Made from crushed and milled marble with polymer and organic binders, these plasters are naturally flexible, so resist cracking, flaking or chipping. They deliver an excellent quality finish that can be painted with emulsion within 24-48 hours, so the team that applies the plaster can also apply the paint finishes. With most RMPs, finishing boils down to four application steps – spray, level, sand, decorate.
Time saver
The savings in time also apply to preparation – the plasters can be sprayed on a variety of substrates, and are effective covering everything from plasterboard and concrete to blockwork. In 99% of applications, no primers or bonding agents will be needed and, because the material is breathable, it is also suitable for lime plasters and cements.
The RMPs now found on the market do not need any direct water on site because they have been mixed in the factory to the ideal consistency for spray application – which also means that the finish is consistent from one batch to the next. Unlike traditional plaster, very little material is wasted on site (less than 1%) and, because there is little mess, there are no slip hazards.
These plasters are breathable and allow backgrounds to release moisture in the building, compared to traditional internal plasters, which also have higher water content. The result is quicker drying times that allow follow-on trades such as carpenters and painters to get on site far more quickly without humidity holding up their work.
Using RMPs also addresses important labour issues. Construction workers are at significant risk from breathing in dust that can potentially lead to permanent disability and early death. Currently more than 500 workers a year are believed to die as a result of exposure to silica dust alone, according to the Construction Dust Partnership (CDP).
RMPs also supply an answer to the skills shortages that the construction industry is experiencing, with many contractors reporting that recruiting skilled, reliable labour is increasingly difficult. Traditional plastering has always been one of the most physically demanding trades on site, with many plasterers prolonging their careers with frequent visits to chiropractors and osteopaths. Few young people now seem to want to enter the trade, hence a skills gap, and these products help fill that gap.
Environmental impact
Another issue that the construction industry is tackling is sustainability, with more clients requiring BREEAM ratings of ‘Excellent’ and most tender documents requiring statements of sustainability procedures. Spray-applied RMPs can also contribute towards reducing environmental impact.
Reducing site water usage during construction, for example, is now seen as one of the key elements of developing sustainable construction. In 2008, the industry accepted that its target was to cut water usage on construction sites by 20% by 2012, while credits are given under the BREEAM scheme for recording and monitoring the consumption of potable water necessary to complete all construction processes.
Using ready-mixed plasters will cut that water consumption easily without any extra measures being necessary – the only water necessary has already been added in the factory. To meet the sustainability agenda, the packaging will also be recyclable, while the pallets will be FSC-certified, so any waste material will require little or no waste stream management.
Transport movements are also a factor in BREEAM and other sustainability assessments, and ready-mixed spray plasters minimise transport requirements because the material is so much more compact than conventional plaster. Typically, just one 25 kg bag will cover up to 20 m² of wall. This reduction in movements of material also contributes to health and safety.
There will always be a need for traditional plastering in certain niche markets but, for the bulk of applications, ready-mixed spray plasters provide a reliable, proven alternative that offers many advantages that are hard to match.
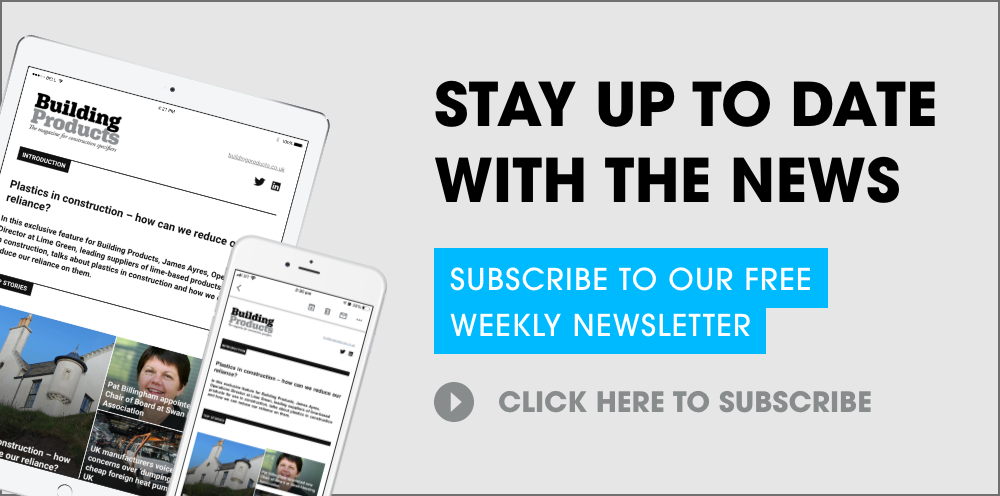