Stone solultions

The use of ventilated cladding has become a popular approach to delivering the desired aesthetic for new-build and refurbishment projects and a stone finish is a popular choice. However, natural stone, such as limestone or granite, is not the only option for delivering a natural stone texture and aesthetic. Alternative cladding materials, including engineered stone and ceramic granite, can also be used to provide a high-end look, along with durability and extended service life. All three ‘stone’ options can also provide materiality in context with the local built environment, offering an ideal solution for extensions to heritage buildings, conservation areas or meeting local planning restrictions.
Whilst the aesthetic results can be indistinguishable, there are numerous technical differences which should be understood as part of a considered approach to façade design and specification.
Natural Stone
There are times when only natural stone will do. For those projects, a stone ventilated cladding system offers the ideal combination of classic tradition and contemporary performance and buildability. Natural stone is also non-combustible and can be specified in complete confidence of its fire safety credentials.
Ventilated façade systems enable the use of natural stone in a contemporary and convenient format that is compatible with lighter building structures. High quality natural stone ventilated façade systems can offer the façade designer scope to enhance the project, providing a wide range of features and detailing to complement the façade design, all prefabricated offsite from the same stone. For example, as part of a recently completed natural granite facade project at The Point data centre at Canary Wharf, integral louvre detailing was also supplied to disguise ground level ventilation vents.
Of course, natural stone is not without its limitations. The traditional ‘clamp and dowel’ fixing systems typically used mean façade panels often need to be at least 30-40mm thick. However, by using a robust, specially designed, fully-anchored alternative, it is possible to use limestone and granite panels as thin as 20mm.
Engineered Stone
For projects where a large ‘stone’ panel size is required, engineered stone provides an excellent alternative to natural stone. Engineered stone panels are cut from solid blocks, so they can even be ‘cut to curve’, to create rounded façades and circular elevations with the appearance, texture and materiality of natural stone. For example, the installation of an engineered stone facade system at Kew Bridge West, an exclusive residential complex in North London, involved smooth and flawless curved façade panels to clad the lower storeys of the development’s two circular towers.
Available in a wide variety of colourways and polished, honed or sand-textured finishes, engineered stone is not susceptible to flaws or fissures. This material allows some manufacturers to produce supersized panels (up to 3050mm x 1240mm x 20mm) that are exceptionally strong and durable, despite a thickness of just 15mm and 20mm.
For all ventilated façade systems, fire resistance must form a key specification criterion and specifiers should not assume that there is a generic classification for engineered stone as varying engineered stone materials will contain different amounts of resins and binders. Each manufacturer should be able to provide system-specific fire testing data to demonstrate compliance with the relevant standard. For example, our engineered stone panels are certified to A2 according to BS EN 13501-1 for fire resistance, which means they are entirely suitable for cladding buildings above 18m in height.
The relative lightweight nature of engineered stone façade panels means that projects involving the use of panels up to 20mm thick and measuring up to 3m x 1m can be installed. Specifiers should consider whether non-sequential installation of façade panels will provide benefits during the build and occupation phase and select an installation system accordingly. Non-sequential installation provides flexibility and speed of installation advantages and allows individual panels to be removed and replaced to access building services for maintenance purposes.
Ceramic Granite
A fully-vitrified architectural porcelain, fabricated using entirely natural constituents, with no binders, resins or bonding agents, ceramic granite opens up a huge array of aesthetic possibilities, ranging from the traditional appearance of natural stone, through to finishes that could be mistaken for natural timber, alongside vibrant colourways and even pseudo-textile finishes, such as leather. For example, at the Kingston Heights residential development in Kingston Upon Thames, ceramic granite in creamy beige and wood effect colourways provided the developer with a low maintenance way to achieve the appearance of limestone and natural oak panelling.
Ceramic granite panels can be supplied in a wide range of standard formats up to 1800 x 900mm, depending on the style and colourway chosen. The largest special production size currently available in the UK is 3200 x 1600 x 12mm. In addition to the design versatility, reduced loading and durability advantages of ceramic granite, selecting this material also provides substantial low maintenance and service life advantages, thanks to exceptional hardness of up to 8 on the MOHS scale – which means that it is as hard as Tungsten and twice as hard as Quartz.
Unlike most types of natural stone, ceramic granite is impermeable, which also contributes to the lifecycle performance of the building. Zero porosity ensures façades are resistant to climatic conditions, including everything from blazing hot sun through to rain, sleet and snow at sub-zero temperatures. Specifiers should also check that the ceramic granite they select complies with all international standards for freeze-thaw resistance and verify that it is resistant to long term weathering, algae growth or discolouration. Again, fire resistance should also be checked for the specific proprietary system selected and a system certified as non-combustible should be chosen for any high rise buildings above 18m.
Design Flexibility
When cladding materials are being specified to match, reference or complement existing stone buildings, or simply to make a design statement of their own, there is a wide choice of materials available for use as part of a ventilated façade system. Consequently specifiers can combine a best practice, contemporary approach to creating a robust building envelope that meets the needs of architects and developers while offering complete design flexibility.
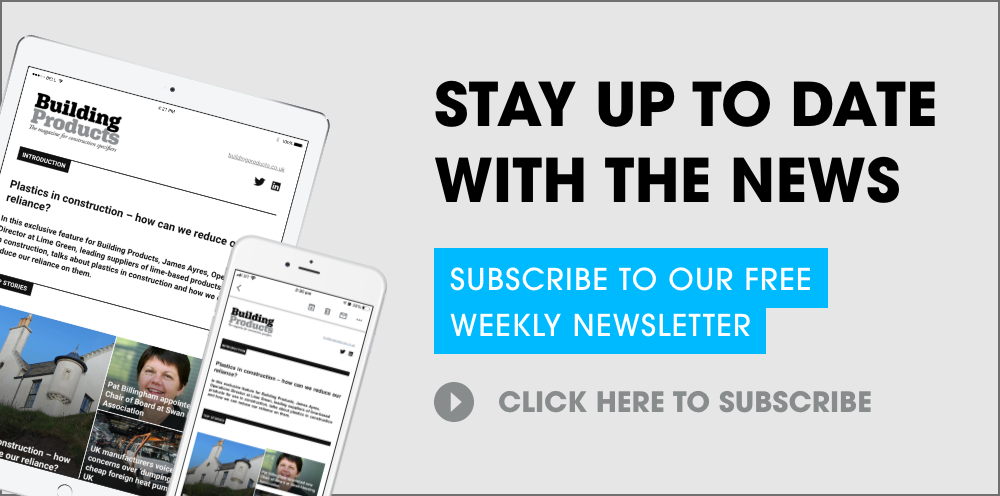