The Wonder of Wood

With its clean, cost effective, attractive and efficient properties, there’s no doubt that timber has a huge part to play in the future of UK construction. The word about wood is spreading: Rowan Moore, The Guardian’s architecture critic, recently dubbed engineered timber “the new concrete” and “a miracle building material” thanks to its ability to extract carbon from the atmosphere rather than add to it.
Ultimate sustainability
As a uniquely renewable building resource, timber is hard to beat in the sustainability stakes. As they grow, trees absorb harmful carbon dioxide, locking CO2 into the wood forever rather than releasing it into the atmosphere. Therefore, trees should only be felled when they have fully matured and stopped absorbing CO2 – allowing the environment to fully benefit. And when forests are responsibly managed by owners who put more in than they take out, you can be sure that the timber you’re using has been sustainably harvested.
Embodied energy is the sum of energy required to create a product or service. In the construction industry, this factors in energy expended through building, production and transportation, typically accounting for around 30-50% of a project’s entire carbon footprint. It takes very little energy to convert trees into timber for construction, while the building process typically requires a fifth of the vehicle deliveries demanded by concrete. These factors give timber the lowest embodied energy rating of any mainstream building material.
For example, a wooden floor beam requires around 80 megajoules (mj) of energy per square metre of floor space and emits 4kg CO2. By comparison, a square metre of floor space supported by a steel beam requires 516mj and emits 40 kg of CO2, while a concrete slab floor requires 290mj and emits 27kg of CO2.
Timber is remarkably strong and durable, guaranteeing no compromise in quality even when speed of construction is taken into account. Timber structures can last hundreds of years and are less expensive and easy to maintain than other materials.
Thermal efficiency
The material’s inherent qualities further enhance its green credentials. As a natural insulator, timber contains small air pockets which limit its ability to conduct heat. This helps minimise the energy needed for heating and cooling homes, which typically leads to less use of fossil fuels. Timber frames also allow more space for insulation than brick constructions, enhancing thermal efficiency.
Easy to work with
Lightweight and versatile, timber is easy to handle and install. This facilitates a faster, less expensive and less disruptive construction process, making it the ideal material for brownfield site construction and urban development – as well as altogether quieter, calmer and cleaner building sites.
Off-site, timber gains points thanks to its ability to streamline the offsite manufacturing process, cutting build time by as much as 50%. A timber frame can be precisely pre-cut and easily put together with less manpower, fewer deliveries to site and minimal debris left behind. Manufacturing in a controlled factory environment also means that the weather is never a problem, it’s less likely there will be any defects, and risk of injury is reduced. And with greater potential to automate more steps of the manufacturing process, dependence on traditional skilled labour is reduced. When it comes to making cost savings, timber construction is a dramatically more cost-effective form of construction than traditional building methods.
The future is upwards
With the benefits of timber being more widely recognised, experts are starting to question whether timber could replace concrete and steel for mid and high-rise buildings. A recent government white paper, Fixing our broken housing market, highlighted the importance of using available space efficiently and avoiding building at low density, especially in urban areas. One of the ways to achieve this is to build up rather than out.
Several trailblazers are already considering this possibility. The Vancouver-based architect Michael Green is one of north America’s leading exponents of wooden skyscrapers. In his TED talk he calls timber “the most technologically advanced material” he could work with and declares that the race is on to create a ground-breaking “Eiffel Tower moment” using wood.
Here in the UK we are making strides in timber construction too. Murray Grove, designed by Waugh Thisleton, is the first tall urban housing project to be constructed entirely from pre-fabricated solid timber. The nine-storey block in north London was put up by a team of four in just 27 days.
Aesthetically pleasing
The natural beauty and versatility of wood is hard to replicate. Timber naturally grows more slowly in colder climates, resulting in tighter growth-rings. This not only signifies stability and strength but also provides an additional design feature. It offers a wide range of aesthetics that give great design flexibility. It can vary in colours and texture, can be painted in any colour, waxed and varnished, carved, cut, glued and nailed or just left as it is. A timber framed building can be one of the most beautiful types of structure possible. Timber can also be clad in external materials, allowing it to complement specific local regulations and planning requirements.
Meeting today’s challenges
At a time when the construction industry is under increased pressure to build quickly and sustainably, timber offers an inspirational alternative construction solution. In a recent survey by the Royal Institute of Chartered Surveyors, 61% of respondents cited labour shortages as a serious constraint to growth. This clearly underlines the need to tackle skills shortages now and look to less labour-intensive production methods. For these reasons and more, I truly believe in timber’s ability to solve the UK’s housing crisis and meet the demands of our construction industry.
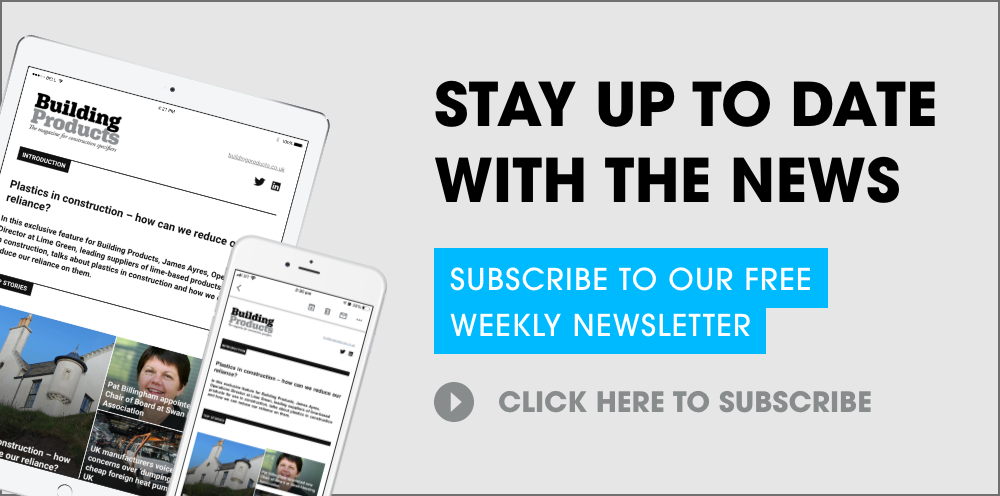