Timber in the frame

Last year, Sajid Javid MP declared a ‘bold and radical vision’ for the future of UK housing.
Set out in the Housing White Paper was a desire to diversify the UK’s housing market. Around 60% of houses in the UK are built by just 10 housebuilders; creating a competitive marketplace will encourage investment in businesses, skills and technology. This diversity translates to far more than SME builders and housing associations. The government says it ‘will support efficient, innovative and under-used methods of construction, such as off-site factory builds’ – welcome recognition of off-site construction.
Fast-forward 13 months, and the changes to the planning rules, announced by Prime Minister Theresa May, in March, emphasised the need for speed: “We’re giving councils and developers the backing they need to get more homes built more quickly…The new rules will see around 80 of the proposals set out in the Housing White Paper implemented, including using land more efficiently, fast tracking planning permissions into homes, giving greater certainty to local authorities and putting plans in place to give communities more control.”
The PM also made it clear that “it’s also time for builders and developers to step-up and do their bit.” The same can be said of building product manufacturers and suppliers as they respond to the demands of the house building industry.
With a reliable supply chain, a respected track record and in many cases, capacity, the UK’s off-site construction industry is essential to building more, high-quality homes, quickly.
Why Timber frame?
Timber frame is a proven off-site construction method, tried and trusted over hundreds of years. Modern timber frame is a far cry from the traditional methods recognised by generations of homeowners. Today, frames are precision engineered, strong and durable. The timber frame represents the basic means of structural support, combined with factory manufactured wall, floor and roof panels. Investment in software, equipment and skills has generated a robust and resilient house building solution.
With cost and time efficiencies, combined with impressive environmental credentials, it’s no surprise that more and more builders and contractors are selecting timber frame as their building method of choice.
Accuracy is an added-value benefit. Build components can be manufactured in factories under a quality assurance scheme while software, such as MiTek enables design teams to send drawings and cutting lists direct to the saws for precision cutting.
Rapid build
Off-site construction enables a rapid build. Managed properly, the build is not adversely affected by inclement weather. A typical three-four bed timber frame kit can be erected in less than a week; ready for roofing. Brickwork is off the critical path, as are any of the facade finishes; it’s simply cladding. With the support of a good roofing contractor, the build can be dry in a week. Add in windows and doors and the building can be weathertight in the same timeframe. Traditional brick and block can take weeks to get to roof level.
Due to the speed of erection the contractor must be organised. While the beauty of off-site construction is exactly that – factory precision manufacturing of quality build components – the real benefit is only appreciated by those who have all their trades organised. What’s the point in a fast construction method if there’s no roofer to make it dry, plumber or electrician for first-fix, or a dry-liner to get the interior fit-out underway? Up-front labour and materials, such as groundworks and scaffold, must also be considered.
Financial reward
The cost of building with timber frame can be off-set against the speed of erection, build it quickly and have the follow-on trade organised and the financial benefit is clear. Off-site construction makes costing more predictable and allows for accurate budgeting. Add to this the management and organisation undertaken by the timber frame supplier rather than the contractor and the positives far outweigh the negatives.
Energy efficiency
The Housing White Paper also acknowledged the importance of energy efficiency and sustainability. It is far simpler to achieve a low U-value with timber frame than traditional build methods. To achieve a U-value of 0.19 W/m2K, a traditional build would usually need a wider wall construction than that of a factory manufactured timber wall panel. It would require a bigger cavity with more insulation and would have a negative impact on room size. On a housing development where every millimetres counts, the space saving can soon add up, providing valuable space to restricted plots.
To comply with Building Regulations a Standard Assessment Procedure (SAP) rating must be submitted, alongside the predicted Energy Performance Certificate (EPC) for new dwellings prior to work commencing. Thermal bridging and air tightness are key indicators in achieving a SAP rating. Timber frame construction can exceed the national standards in both instances; for example, some manufacturers can achieve an average Y-value of 5%, a 3% improvement on the national standard. The lower the Y-value, the less heat is lost from the structure. Airtightness can be designed into the building fabric helping to save energy and reduce household bills across the lifetime of the property. The Structural Timber Association encourages the use of timber from PEFC or FSC certified sources.
Possibility
With renewed interest in this global construction method, timber frame manufacturers are seeing a shift in requirements as leading housebuilders and contractors realise the benefits of building off-site in timber. They are beginning to demand more from their timber frame suppliers, such as factory-fitted windows and improvements in thermal performance. Yet, parterships between builder and manufacturer are allowing R&D to flourish, as both parties explore the possibilities of timber frame construction.
The housing crisis is an opportunity, which the builders and manufacturers of the UK must embrace. There’s never been a better time to unlock the potential of timber frame construction.
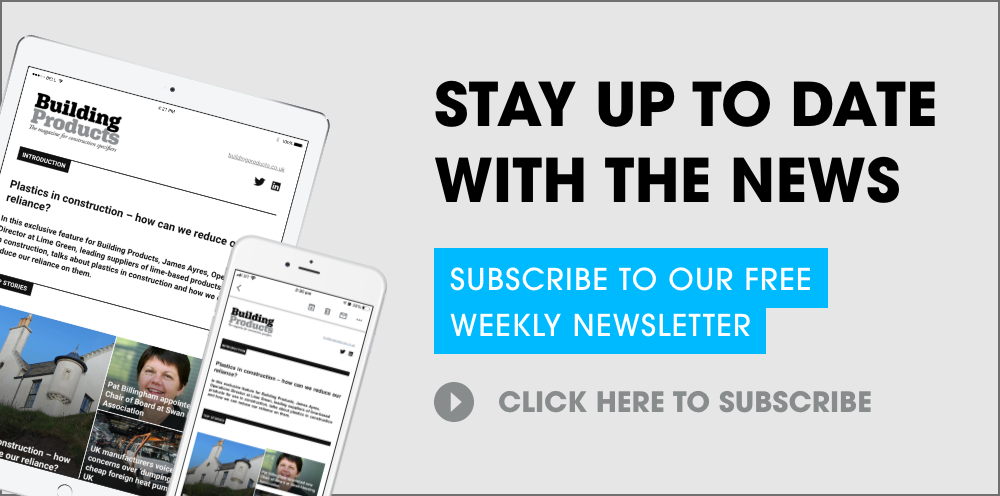