UK volumetric construction market increases by 6% in 2017

The UK market for prefabricated volumetric modular buildings and portable accommodation is estimated to have increased by 6% in 2017 – a ‘significant’ improvement on 2016, when there was a dip in market value, possibly a reaction to the EU referendum. The market value includes factory-made, fully assembled three-dimensional modules, but excludes bathroom and kitchen ‘pods’. Products are broadly split between permanent and semi-permanent buildings and temporary or portable accommodation.
Since the start of the recovery in the construction industry in 2013, demand for volumetric construction has improved, in part due to increased demand for site accommodation on major infrastructure projects e.g. the Crossrail and Thameslink railway construction programmes, plus recovery in other sectors such as offices and education.
The biggest market for volumetric products is temporary accommodation on construction and industrial sites and event hire, while education and healthcare are also key areas of use. The ranges of uses are extensive, with operating theatres and wards probably being the largest application in the healthcare sector, for example. In the education market, semi-permanent school classrooms are probably the biggest use of modular buildings, and in some cases semi-permanent education buildings also end up being permanent structures. Major permanent builds include sixth form blocks, specialist subject blocks, sports facilities and whole nurseries.
A number of established construction and housebuilding companies have begun to diversify into offsite housing in recent years, with more established players including Laing O’Rourke, Berkeley Homes, Mace, Barratt Homes and Crest Nicholson. There have also been several new market entrants from other market sectors over the last couple of years.
Over the next few years, there are several factors that are likely to underpin steady growth in the sector, probably over and above the forecast for the overall construction industry. These include an increasing number of public sector procurement frameworks several of which are specific to offsite construction and increasing use of Building Information Modelling (BIM). More importantly, there is now a strong likelihood of an increase in the use of volumetric and other types of offsite construction methods to help meet the chronic housing shortage and cope with the lack of traditional construction skills within the construction industry.
In the Housing White Paper in February 2017, the government supported the use of offsite manufacturing techniques, recognising the main benefits of this type of construction: high quality, reliable, more productive, energy efficient and requiring fewer people onsite. The government’s £2 billion Accelerated Construction programme and £3 billion Home Building Fund both support local authorities, SMEs, custom-builders and innovators to develop land for housing, including those using modular construction schemes.
High levels of demand for site accommodation on major infrastructure projects are also likely to be sustained through to 2022 and beyond through the implementation of the government’s Roads Investment Strategy and the continuation of the Smart Motorways programme. Between 2017 and 2022, the market is forecast to grow at a rate of 3-5% per year.
The drive towards sustainable development, coupled with the need to meet energy efficiency and carbon reduction targets, would also seem to weigh in favour of volumetric construction. Compared to traditional construction, volumetric building methods typically generate less waste, typically have superior airtightness, and hence thermal insulation performance, than either brick and block and timber frame construction.
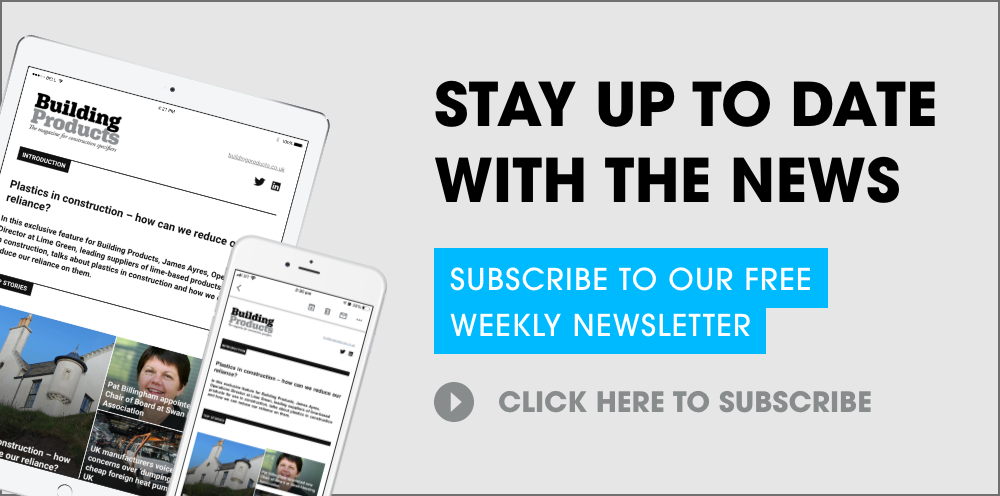