Wet room ventilation
Without the right ventilation solutions in place, removing the high levels of moisture and excess heat that kitchens and bathrooms produce is nearly impossible. If condensation isn’t effectively dealt with, it will inevitably lead to mould and damp.
In a recent YouGov survey, 58% of respondents stated that they suffer with mould or condensation problems in their home. Dampness is a recurring problem within the UK, and unfortunately many still assume that it is an unavoidable occurrence within wet rooms. However, as specifiers will know, there are plenty of solutions that can help prevent the damaging effects of condensation on building materials.
Condensation forms when the temperature of a surface is below the dew point of the surrounding air, which leads to streaming windows and walls. High levels of moisture and relative humidity combined with possible breeding places, such as wood, carpet or wallpaper, will almost certainly lead to the growth of microscopic mould spores, which can quickly spread from wall cavities and small crevices throughout the entire room. This will leave permanent unsightly and unpleasant marks on the building fabric.
“When choosing a sufficient ventilation solution for a wet room, it’s important for specifiers to consider the benefits of utilising dMEV technology”
In addition, without effective ventilation, a plethora of unhealthy pollutants caused by everyday activities, such as cooking, cleaning and the accumulation of rubbish can occur. Apart from having to deal with unnatural smells, occupants will also be at risk from developing respiratory or dermatological conditions. It’s a worrying statistic that over 80% of people are at risk of suffering from the effects of unhealthy air, and it’s something that specifiers have a responsibility to try and take action against.
Under Approved Document F in System 3 of the Building Regulations, specifiers must commission a ventilation system with varying trickle flow rates in the wet rooms of a home: 6 l/sec for toilets, 8 l/sec for bathrooms and utility rooms and 13 l/sec in the kitchen. D-centralised mechanical extract ventilation (dMEV) fans are the ideal solution as they provide a preventative form of ventilation – continuously extracting humid, moist air, as opposed to traditional intermittent ventilation systems, which work by being manually switched on.
Specifiers are advised to look for fans that are fully compliant with trickle flow regulations, and have an everyday running rate that can be set by the installer. For rooms with extremely high humidity levels, fans that have a boost speed feature to up the trickle speed to 20 l/sec, which can be activated manually by pull cord or remote, or by an intelligent humidity sensor, is another essential function.
High-end performance
It’s also important for specifiers to think about the additional features that ‘best-in-class fans’ have to offer in protecting the building materials from decay and increasing the overall efficiency and appeal of a wet room.
Small and stylish devices that can be quickly and easily installed to the wall or ceiling anywhere within zones 1 and 2 in the bathroom, and zones in the kitchen, can suit the aesthetics of any wet room. Additionally, with homeowners becoming increasingly aware of their environmental impact, it’s also important to consider ventilation solutions that consume a minimal amount of energy. Specifying a fan that has extremely low running costs and produces operation noise levels at around 10 dB (A) is therefore also advantageous.
When choosing a sufficient ventilation solution for a wet room, it’s important for specifiers to consider the benefits of utilising dMEV technology. Choosing the right fan is also critical. Therefore, specifiers are advised to look at the additional benefits of the fan to determine whether it’s the best option to help increase the lifecycle of new-build or retrofit bathrooms and kitchens, protect against the deterioration of building components and materials, and nullify toxic gases amassing within the home.
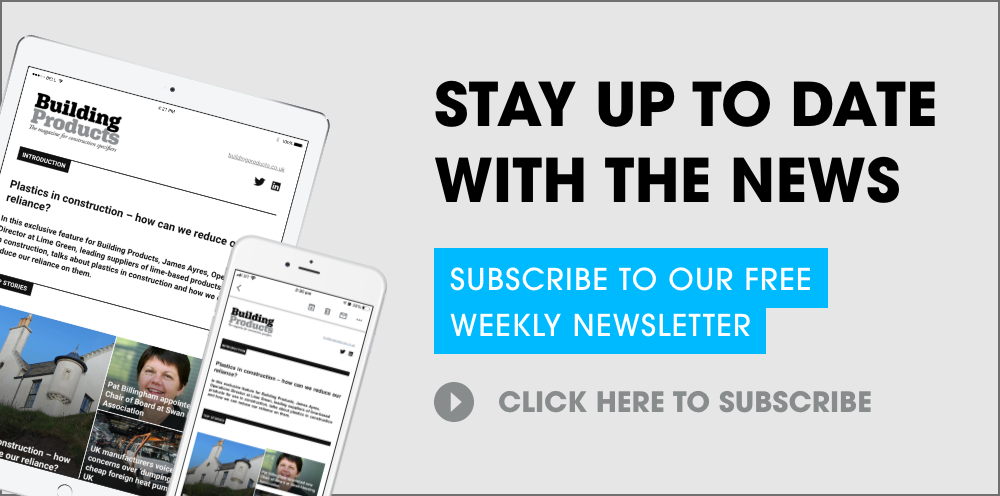