What’s the reality for those on the ground in the building products sector?
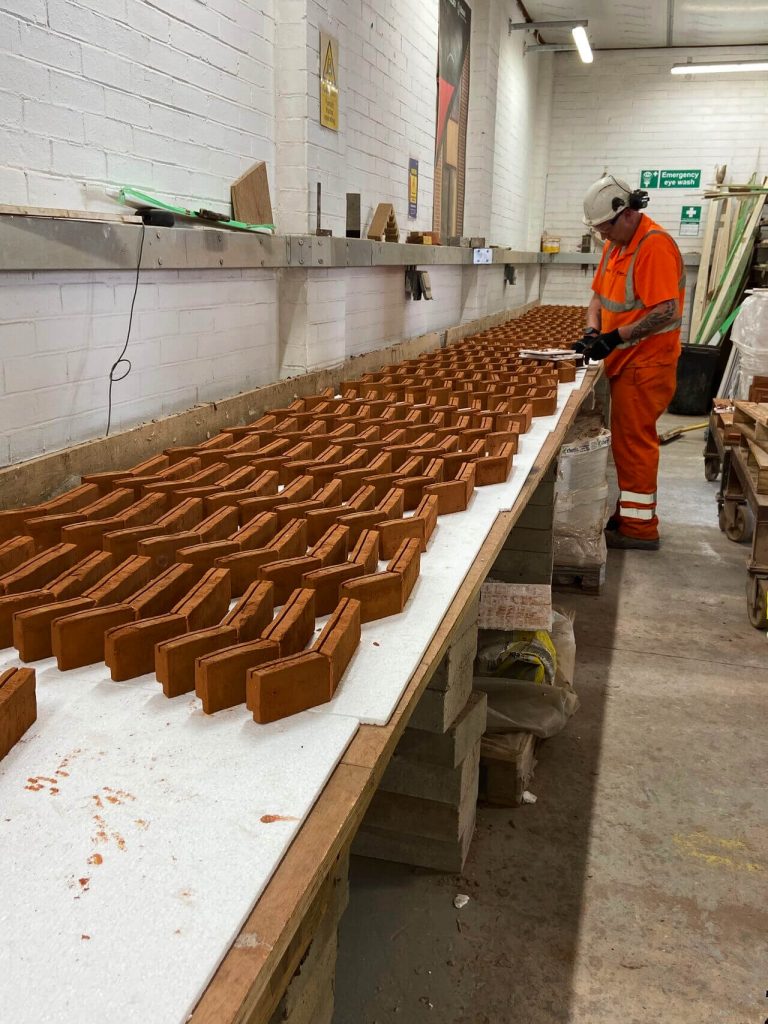

In this special Building Products Magazine feature, we talk to businesses and leaders in the sector to get their take on Brexit and the impact it is having.
When it comes to Brexit, it is important to distance yourself from the partisan political camps of leave and remain and look at the actual reality of what is happening.
The arguments from those in camp leave or remain are so polarised that you cannot help feeling that the reality of what Brexit will mean for the UK is somewhere in the middle. You can spend hours, months and years talking about the vote and whether we have the best deal. Instead, this article will look at what business owners in the sector are feeling right now and whether they are experiencing some of the challenges that they were told they would face.
Paul King, Marketing Director at Vicaima – a manufacturer and supplier of interior timber doors and wardrobes. The business has a manufacturing facility in Portugal and Paul says that planning has been key to ensuring business continuity.
He explains: “We had been preparing for the end of the transition period well in advance of this January. We had taken the opportunity to review all possible scenarios, including the potential for material shortages and I am pleased to say all this forward planning paid off. At the present time we have experienced no interruption to our shipments and with a stock holding at our Swindon, Wiltshire base in excess of 100,000 doors, we are successfully supplying developers and contractors nationwide.”
So far so good then for Paul and his business, and he is positive about the future too.
He says: “It is likely that additional UK regulation will be introduced and is to be expected. However, in respect to performance standards, especially for products such as fire doors; our rigorous testing regime to UK criteria is likely to see further opportunities for the company. Having been based in the UK since 1988, we are confident specifiers will value manufacturers who truly understand the local market, rather than speculative importers with no vested interest.
“Also, for those concerned that a departure from Europe somehow means an end to European design influences, Vicaima can assure specifiers that its very much a case of new doors for a new age. Innovation is at the heart of what we do and with a presence in more than 30 countries worldwide, we are constantly monitoring new trends and ideas for the benefit of the UK market.”
So far, so good
It is a case of so far, so good too for Paul Richards who is the Managing Director of Aquarian Cladding, which is a specialist supplier of external brick and terracotta cladding systems.
He says: “We’ve been making deliveries into the UK from the beginning of the year and all have arrived on time, and to our customers satisfaction, so I can only describe it as being ‘so far so good’.
“As any sensible business should, we’ve had ‘Managing Brexit’ on our agenda for a very long time. We have taken it very seriously and therefore planned for it for well over a year, taking external legal, financial and logistics advice throughout.
“Like many businesses, we have had our fair share of fear and concern about its potential impact on the business, especially as we were never going to truly know to what extent until we loaded a lorry in Belgium and sent it off to the UK. Our team has worked closely with our supply partners to manage and avoid any problems on the way. They deserve full credit for getting the lorries through and arriving on site on time. So, for us it is a case of so far so good.
“We are taking nothing for granted though, as there are suggestions that we are not yet out of the woods. January has been relatively quiet, due to stock imported and stored pre-2021, so the roads and ports will get busier.
“In addition, full customs declarations for construction products are not required until July, which may also lead to delays. That said, we feel we have now got a good handle on what’s required to bring materials through.”
Positive sentiment
Paul says he is generally positive about the future too but does see some challenges.
He explains: “The fresh produce guys are struggling more than those of us importing construction materials, so we shouldn’t underestimate we’re in a slightly different position.
“From a logistics perspective, it is not as bad as I first feared but we prepared ourselves for the worst. I would like to think that is why the impact has been negligible for us so far, but only time will tell.
“One thing for sure though is there are additional fixed costs associated with processing import and export paperwork. As a result, the transport cost has increased by approx. 10% for a full load and someone must pay for that.”
76% of products made in the UK
It is interesting to hear from Paul Richards and Paul King about how steady it has been so far but with the consideration of potential challenges – and busier times – to come.
To try to extrapolate the assessment of sentiment further, Building Products also spoke to Noble Francis, who is Economic Director at the Construction Products Association – which represents hundreds of companies in the sector.
In how his members are reacting, Noble says: “It’s clearly early days as the Brexit implementation period only ended on 31 December and it is worth remembering that 76% of products used in UK construction are made here. Of the products that are imported, two-thirds are imported from the EU. Some firms had built up stocks to deal with any potential disruption that may occur in January.
“There were products in which demand exceeded supply even before the end of last year due to the rapid recovery in house building, refurb and DIY after the first lockdown. In addition, there were already delays at some ports before 31 December due to capacity issues and Covid-19 safety issues. As yet, we have not been made aware of new products supply issues as a result of the end of the Brexit implementation period, it is still early days and construction activity tends to be quieter in late December and early January.
“The complexity of the UK-EU Free Trade Agreement means that there remain issues on rules of origin – and whether manufactured goods qualify as locally sourced – as well as the mutual recognition of conformity assessment or test results in which the changes will occur on 1 January 2022, so the Brexit issues and impacts are not over yet for industry.”
On the longer-term impact, Noble says: “Longer-term it may change the distribution of supply chains. For some imported products, the increase in admin and certification costs may mean that there may be UK substitutes that will prove easier to source, whilst for some other imported products changes in the UK’s global tariffs may mean a shift away from the EU to other countries where it is cheaper to produce and now have a lower tariff.
“However, for the vast majority of imported products, the end of the implementation is unlikely to make a major difference apart from raising costs due to additional admin and certifications, plus potentially higher shipping costs.”
Skills
One of the issues that has been bubbling in the sector is skills and access to labour; and whether a decline in workers from the EU is causing problems.
Noble says: “There were already issues around EU skilled labour in construction even before the end of the implementation period, particularly in London which is the region most reliant on non-UK construction labour. The number of EU construction workers in London has fallen by 54% since 2018 Q2 due to workers going home and not coming back or being replaced by others coming from the EU. It is too early to tell the extent to which this will be exacerbated by the new points-based immigration system, but it will undoubtedly make bringing people over from the EU considerably more difficult given that the system is employer sponsored, whilst 41% of workers in UK construction are self-employed.
“In addition, 86% of construction workers are in small and medium-size firms, which are the least able to sponsor workers to come over due to the cost and admin burdens involved. House building and refurb activity is currently higher than pre-Covid-19 but, overall, construction output is still lower than it was before the pandemic. If construction output returns to pre-Covid-19 levels or surpasses it, where will we get the skilled construction workers from?”
Resurgence of British products
Moving back to how businesses themselves are coping, Stuart Dantzic, who is Managing Director of Caribbean Blinds, says that Brexit has been a positive for the business and is seeing renewed interest in British made products.
He says: “Despite the initial delays in raw materials coming in from abroad, which we had expected and factored in to our model by increasing our stock holding pre-Brexit, Brexit has been positive for our business for a number of reasons. The key for us is that both our trade partners, along with end consumers, are actively looking for products that are made in Britain, rather than shipped in as a ready-made product from abroad.
“The origin of manufacture is a key purchasing factor – UK made products for consumers not only mean they are supporting the economy (which is on everyone’s minds with the pandemic), but also guarantees them shorter lead times, reassures them of high-quality construction and, above all else, great service. They are dealing with businesses and people based in this country which makes a big difference, whether for initial advice or after sales service if a part needs replacing.”
Stuart also says he is wholly positive about the future for the sector in this new Brexit context.
He explains: “The slight headache of additional admin is far outweighed by consumers desires to buy British and all its associated values. I also believe that over time, as businesses evolve in the UK, there will be more partnerships created (businesses working together to grow), and UK businesses will look to source raw materials from within the island where possible.
“I would also say that the combination of the global pandemic and Brexit has actually provided a great opportunity and boost for not just the shading industry, but the whole home improvement sector.
“With the stay-at-home mantra and holidays abroad cancelled for the time being, the focus is on our homes, which have become our whole world, and with consumers also wanting to buy British made products there has been a boost for the sector that I do not believe will slow down anytime soon.
“Furthermore, monies invested in homes and gardens will show consumers a return when moving (or re-mortgaging) and I believe there will be a new mindsight going forward; consumers making considered purchase decisions and ditching long haul flights & holidays, for creating a holiday destination right there in their back gardens, that can be enjoyed and utilised 365 days a year.”
Conclusion
Certainly, it is early days, but Building Products Magazine is positive about the early signs for the sector and the positivity that those who are making and selling products are feeling.
Yes, there is likely to be challenges and more time is needed to assess the situation fully, but you can’t help but feel the chasm between the academics and commentators who predicted Armageddon for the UK economy and those on the ground living the reality is edging a little wider.
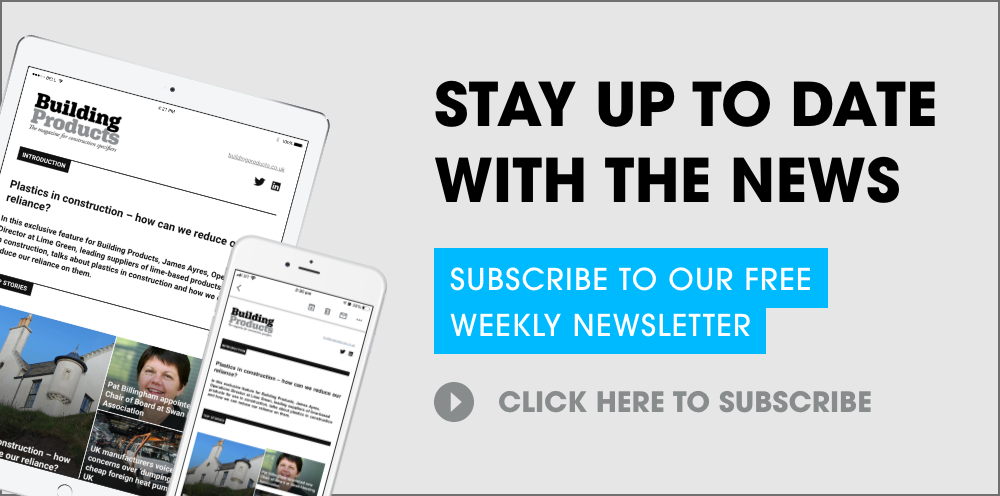